【ものづくり日本】強さの本質をとらえて働くには?―働きがいに困らない未来の業界研究(中)製造業編
最終更新日:2021/07/29
「これからどんな業界が成長し、どこで働けば『一生食べていけそう』なのか」――。そんな永遠のテーマを探る「働きがいに困らない未来の業界研究」。2回目は、日本企業が今も強みを発揮できていて「ものづくり」に関する業界――成長の余地がまだまだある「素材」や「部品」、将来性が大いに期待できる「ロボティクス」などを取り上げます。
この記事を書いた人
「聖火台」に見る日本「ものづくり」の強み
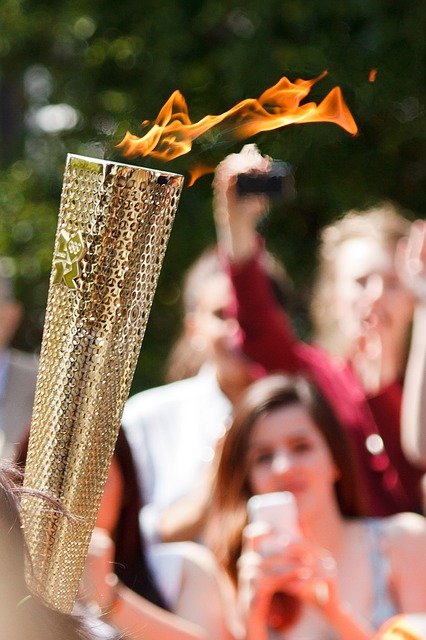
前置きが長くなりますが、「ものづくり日本」の強みについて、まずは考察させてください。
コロナ禍による1年の延期を経て、7月23日にようやく開幕した東京オリンピック。テニスの大坂なおみ選手が聖火の最終点火者に選ばれましたが、その聖火台をご覧になったでしょうか。
開・閉会式の演出・企画チーム統括だった狂言師の野村萬斎氏が打ち出した「太陽の下に皆が集い、皆が平等の存在であり、皆がエネルギーを得る」というコンセプト。それに基づいてデザイナーの佐藤オオキ氏が率いるデザインオフィス、nendo(東京都港区)がデザインしたのが「TOKYO2020」の聖火台です。
オリンピックなどの時代の象徴となるような国際的イベントでは、開催する国の技術の「粋(すい)」が活用されます。nendoのウェブサイトによると、今回の聖火台は、五輪の5大陸にちなんで5枚のパネルを上下2段に組み合わせて構成。そのパネルが閉じていると外観は全くの球状に見えます。そこに、聖火を灯そうとした時につぼみが花へと変化するように開き(咲き)ました。「太陽から得られるエネルギーや生命力」を表現したのだそうです。
球の直径は3.5メートル、重量は2.7トン。花のように開く外装パネルにはアルミ素材を使用。10ミリ厚のアルミ板を特殊成形して、切り出すときに熱で変形しないようにレーザーで形状を測定しながら加工しました。強度が必要な箇所は7mm厚、そうではない箇所は4mm厚に切削して軽量化も図りました。
耐熱試験と耐風試験は繰り返し行われ、さまざまな状況下においても振動や誤差が起きないように、チューニングが施された。その結果、動作中のパネル同士のすれ違い幅が最も狭い箇所で3mm以下程度という精度の高さと、スムーズな動きが実現した。
※nendoのウェブサイトより引用
素材と部品と「すり合わせ」に強い日本
聖火の炎には燃料として水素を使用。水素は燃えても無色透明なため、彩りよく燃え上がらせる仕掛けとして、炭酸ナトリウムをバーナー付近から噴霧させているといいます。「薪をくべたようにゆらめく炎の動きと形状」になるように調整したのだそうです。
これらは単に「職人技のすごさ」というだけでありません。戦後の日本が工業化に突き進んできた中で、高いレベルで実現してきた「素材」「部品」の技術と、「すり合わせの力」とも呼べる日本ならではのアドバンテージが、世界的に競争力の高い「ものづくり」の力として発揮されてきたからです。
素材や部品の強さは、半導体産業を見るとわかりやすいでしょう。半導体とはLSI(大規模集積回路)とかマイクロプロセッサー、フラッシュメモリーなど、デジタル機器には欠かせない部品です。1970〜80年代は「DRAM」とよばれるメモリー製品で、日本企業は世界を圧倒してきました。しかし現状では、世界的に優位な日本の半導体メーカーは少なくなりました。
80年代後半にパソコンが普及し始めてから、ほぼ故障しない日本のメモリーはコストが高くなり、早いサイクルで買い換えるパソコン向けに数年でダメになるが安価なメモリーを製造した韓国・サムスン電子などに追い上げられました。メモリー以外の半導体製造でも、台湾のTSMC(台湾積体電路製造)などが微細な製造技術を磨き、今では磐石な地位を築いています。
半導体を製造するのには様々な工程が必要で、ナノメートル単位で微細な加工をしなければなりません。そのため、非常に純度の高い素材や、そうした加工を可能にする半導体製造装置が十数種類も必要になります。この半導体製造装置でいえば、5〜7種類については、東京エレクトロンやアドバンテストなどの日本企業が世界のトップシェアを占めています。
半導体製造装置では世界トップの米アプライド・マテリアルズやオランダのASMLなどの欧米にも大手が多いのですが、その欧米系の装置でも中に使われている部品は60〜80%が日本製であるのが実態です。
そして半導体のそもそもの素材であるシリコンウエハーをはじめ、加工・成形に必要な様々な薬剤、金属素材などでも、高純度のものを提供できるのが日本企業の強みでもあります。多くの分野で50〜90%というシェアを誇っています。
「優位な人材」の不足が深刻になっている製造業
ある半導体製造装置メーカーのトップは「これからDX(デジタルトランスフォーメーション)が進み、世の中のほとんどのものがネットにつながるIoTの時代になると、半導体はいくらあっても足りない時代が来る。それに伴い、人材確保も難しくなっていく」と話していました。すでに自動車などでも半導体が大量に使われる時代となり、半導体業界では生産能力のひっ迫が問題になってきています。「半導体がないから自動車が作れない」というニュースを見たことがある人もいるでしょう。
一般に、世の中に出回っているほとんどの製品は、設計の概念(アーキテクチャー)として「組み合わせ型(モジュラー型)」と「すり合わせ型(インテグラル型)」に分けられる、とされています。モジュラー型の代表例がパソコンです。CPUなどの心臓部、キーボード、モニターなどがそれぞれ機能的に独立していても、インターフェースを共有してそれぞれをつなげれば動かすことができます。それぞれの機能を高性能化したり、安くしたりすることで、自在に組み合わせることができます。
一方、すり合わせ型の方は「全ての機能を高度に統合する総合力」が求められる製品です。典型が自動車でしょう。それぞれバラバラの機能をただ集めてつなげても、自動車の基本性能である「走る、曲がる、止まる」は簡単に実現できないうえ、とても危険で走行できたものではありません。どんな部品を使い、機能を高度化し、エンジン、シャシー、サスペンション、タイヤなど全体を統合しないと安全な製品はできません。
日本がものづくりで強いとされるのは、この「すり合わせ型」です。それを支えているのが「各機能を統合的に組み合わせて高度にできる素材や部品の技術力」なのです。日本の自動車産業が強いのは、「カイゼン」のようなシステムに加えて、素材や部品がそれぞれ技術的に高度なレベルにあり、それを統合することで「壊れにくい安全なクルマ」を生産できるからでしょう。
逆に、パソコンや家電などのエレクトロニクス産業で日本メーカーの強みが失われてきたのは、デジタル化が進み、モジュラー型が中心となり、「すり合わせ力が不要」となってきたからともいえます。
「デジタル×すり合わせ」が今後20年のカギ
自動車も半導体が欠かせなくなっているように、これからは「電子化=デジタル化」が進むことで、日本のすり合わせ力を発揮できる分野が狭まっていく可能性もあるでしょう。今後20年間では自動運転などの技術も一般化してくると予想されています。ただ、その時にも「走る、曲がる、止まる」と「安全性」を担保するには、社会全体で必要な技術を統合する「すり合わせ」が不可欠になります。
全体を統合できる際に強みを発揮できるように、素材や部品の高度化やイノベーションは今後ますます重要になります。日本では、主に「BtoB(企業から企業へ)」の製造業で、ますます優位な人材が必要になるでしょうし、職人技のような加工技術を持っている中小企業でもデジタル化に対応できるような人材が欠かせなくなります。米国や中国、ドイツが未来型インダストリーを在り方を探ってデジタルシフト=DXを強化しています。日本も国際競争の中では、DXやIoTによる製造工程の改革や人材不足を自動化で補うためにも、デジタル化人材がこれからも重視されます。
そして、自動車以上に高度な「すり合わせ力」が求められるのがロボティクスの分野です。ロボットも、複雑な動きや高度に精度の高い作業が必要になればなるほど、多数の部品の組み合わせを統合しながら、高度なソフトウエアを融合させなければなりません。
自動車業界では今、「Connected(コネクテッド=つながる)」「Autonomous(自動運転)」「Shared(シェアリング)」「Electric(電動化)」の4語が重視されています。それらの頭文字をとって「CASE」(ケース)とも表現されますが、これらCASEの各要素はロボット分野でも重要になっています。
素材・部品の高度化とともに、すり合わせ力で人間の仕事や生活を支えるロボティクスや自動運転(これもある意味でロボット化)の分野を開拓できる地力が、日本にはまだあります。それを、いかに量産化して普及させていくかが、今後20年の勝負どころになってくるでしょう。それにつながる各種の仕事は、製造業ではこれからのメインストリームになっていくに違いありません。